BUILDING SCIENCE
AIR BALANCING
Well-designed heating and air conditioning systems begin with a calculation of how much conditioned air should be
delivered to each room (a Manual J load calculation). An airflow hood [see Air Flow Hood, below] then shows if the
designed cubic feet per minute of air flow has been achieved. When each room is receiving its proper share, the
system is considered "balanced" and the home will be experienced as more comfortable.
AIR CONDITIONING/HEATING SYSTEMS
The most complex system in most homes is the heating, ventilation, and air conditioning (HVAC) system.
It is composed of three parts - the equipment, controls, and the system that distributes the air.
-
Equipment
-
Central, Forced Air, Split Systems
The most common type of system in the United States is
the central, forced air, split system. It is central because the
equipment serves a number of rooms (as opposed to
window units for each room). It is forced air because
a relative large central air handler (fan) forces conditioned
air through a distribution system to each room. It is a split system
because its major components are located in different places, a condensing
unit outdoors that releases heat collected from the house
and an indoor evaporator unit that cools and dries the air
that passes through it. Both units have coils that effect the
heat transfer.
-
Packaged System
These have both the condenser and evaporator coils in a
single box outdoors.
-
Mini-Split Systems
These combine features of room air conditioners and central split systems.
There is usually a single condensing unit outdoors, connected to multiple
evaporator coils and fans in each room. There are usually no ducts, so there's
no heat gain or loss through a distribution system. The temperature
(and sometimes the humidity) of each room that has an evaporator coil can
be controlled independently, which fosters saving energy in rooms that are
not in use. Ductless mini-split systems also do not create the house pressure
imbalances (and unwanted air infiltration) generated by ducted forced air
systems. Because they allow individual room temperature control, put the entire
system within conditioned space (rather than in a 140 degree attic), have no
distribution losses, and do not cause infiltration and exfiltration, many consider
them the way of the future. Unfortunately, most HVAC contractors have little
experience with them.
-
Heat Pumps [see Furnaces, below]
-
Furnaces
There are several different approaches to heating a home.
- Gas Furances
In these units, a fan blows air over a heat exchanger, which is heated by natural gas or propane
burning within it. The heated air is then circulated through a distribution system to each room.
This is a very popular system in hot, humid climates, particularly now that natural gas prices are relatively low.
- Electric Furnaces
In these systems, air is blown across metal wires that are heated by electricity flowing through them,
similar to the heating elements in a toaster. Heating units using these "heat strips" are the least expensive
furnaces to buy and the most expensive to operate. Their energy efficiency is abysmal and often results in winter
electric bills as high as summer ones in the Deep South.
- Heat Pumps
"Heat pumps are actually two furnaces packaged in the same unit. The first furnace is a compressor system that moves heat
from the outdoors to indoors during the heating season using a refrigerant. The second furnace is an electric resistance heating
unit like those found in electric furnaces. Heat pumps are the most efficient types of electric heat, particularly for the southern
U.S. When they're properly installed, heat pumps can deliver 1 1/2 - 4 times more heat energy to a home than they consume in electrical energy. This is possible because heat pumps move heat rather than making heat from burning a fuel."
[Quoted from Residential Energy by John Krigger and Chris Dorsi, arguably the best introductory book around on
residential energy efficiency and building science.]
- Heat Pumps are not only furnaces. They provide cool air as well, just as
air conditioners do. Like A/Cs, heat pumps have two heat exchanging coils,
one indoors and one outdoors. In addition, they have reversing valves that
allow refrigerant to flow in opposite directions - one way for cooling and one
for heating. In summer, the heat pump takes heat from the house and transfers
it to the outdoors; in winter, it takes heat from the outdoor air and transfers
it indoors. When it's really cold and there is very little heat in the outdoor
air, the heat pump's backup electric coil activates to provide heat.
There are two types of heat pump.
> Air source heat pumps use the heat of the air to provide heating and
cooling. Most of the units in use today are of this type.
> Geothermal heat pumps are considerably more expensive, but much
more energy efficient. These heat pumps collect the earth's heat in
underground pipes filled with water (ground source heat
pump) or use a body of water's heat directly, from a well, a lake, or bayou (water source heat pump).
-
Fans
Central forced-air cooling and heating systems must have air moving through them and this is provided by large centrifugal fans
located inside the indoor heating/cooling equipment. These fans move about 400 cubic feet per minute of air per ton, so a 5 ton unit
is moving 2,000 CFM through the system. That's a lot of air movement and is one cause of unbalanced house pressures created by
forced air systems.
Each fan is designed to operate efficiently if it does not encounter too much resistance. This resistance to flow is caused by many
things, including clogged filters, dirty evaporator coils, bends and constrictions in the ductwork, duct systems with runs that are too
long (which increases the square inches of surface resistance), ceiling grills that homeowners have shut, etc. This is one reason that a well-designed and installed duct system is important. Resistance to flow is called "static pressure" and every fan has a maximum
static pressure it is designed to push against. If it is working against more than its design pressure, the fan slows down and moves
less air. Less air flow means reduced Btu that are delivered in heating or removed in cooling, so reduced air flow makes a big
difference in your comfort. For you techies, here's the formula:
Delivered Btu = Volume of air delivered (CFM)
x
Change in air temperature through system (Delta T)
x
Heating or cooling constant at sea level (1.08 or 4.5)
The types of fans currently in use are constant speed, two speed, and variable speed fans. The better variable speed fans have a
wide range of operating speeds, which depend on how much heating and cooling the thermostat is calling for. In a high-end
communicating system with a compressor capable of operating at different speeds, the outdoor unit and indoor units are synched
together to deliver heating and cooling with maximum efficiency.
-
Distribution System
This is the system that distributes conditioned air in central forced-air heating and air conditioning systems.
Air is heated or cooled, enters the supply plenum, and flows through ducts to the ceiling registers in each room.
-
Hard Ducts
These ducts are formed with sheet metal, with sections fastened together with screws, sealed at the
seams with mastic, and then covered with insulation - or they have insulation on the inside.
-
Flex Ducts
This more common type duct is composed of a thin layer of flexible plastic stretched over a
metal wire coil and then covered with R-6 or R-8 insulation.
Duct systems always leak - it's simply a matter of how much. Using expensive electricity to condition air - and then
leaking it to uninhabited spaces like attics - can be very wasteful. HVAC contractors rarely test
the tightness of their distribution systems, which is done with specialized equipment called a "duct blaster,"
which measures the leakage in cubic feet per minute at a pressure of 25 pascals.
The insulation around ducts is commonly R-6 and much less frequently, R-8. R-8 insulation does not cost
much more than R-6 (and is a 33.3% increase in insulating value), so it is a good idea to upgrade to it. When
you think about it, even R-8 insulation is pretty dinky. Building codes require we put R-30 insulation between the
attic and the conditioned rooms below, yet we put only R-6 insulation between our expensive cooled air and
the 130 degree F attic through which it runs. The most knowledgeable HVAC person I've met (a Ph. D. engineer from MIT
and founder of the National Comfort Institute) wrapped R-19 insulation around the ducts in his own attic.
-
Controls
The gizmo that controls a central heating and cooling system is the thermostat, an automatic switch
that responds to changes in temperature at the spot where it is located. There is a temperature
sensing mechanism inside the thermostat, usually a coil or strip made of two metals that expand and
contract at different rates, causing the bimetal element to move in one direction when the
temperature drops and in the other when it rises. This physical movement actuates the switch to
turn the system on and off.
Programmable thermostats combine a clock and a thermostat, enabling a homeowner to set the
thermostat to choose what the temperature will be in the house at different times of day throughout
the week. The thermostat communicates with the rest of the system to turn it off and on to
achieve the program set by the thermostat. Because homeowners are able to order the system to
maintain energy efficient temperatures in the house when it is unoccupied - and then turn it on shortly
before the family returns home - programmable thermostats are billed as energy savers. This is
usually not the case, as most people with programmable thermostats don't know how to use them.
In response to this, thermostats are coming into the market, the NEST, for example, that memorize the homeowners settings at different
times of day and days of the week - and then start programming themselves automatically to duplicate this usage pattern.
Please note that thermostats respond to changes in temperature, not to temperature and humidity. This creates a potential problem,
especially in hot humid climates. If the air conditioner is oversized (too big), it can quickly cool the house down, reach the thermostat set-
point, and turn itself off. This is called short cycling. It can result in the A/C not running long enough to take enough moisture out of the
air, which can lead to excessive relative humidity and eventually to moisture problems in the house.
AIR FLOW HOOD
This scientific instrument measures the amount of airflow, in cubic feet/minute, coming out of each air conditioning
ceiling register (grill) and verif that the system is balanced and rooms feel comfortable.
APPLIANCES
The household appliances that have the greatest impact on energy consumption are those that run the longest or
consume the most fuel while they are running. In the first category are refrigerators and freezers, whose electric
motors run about 12 hours a day. Older refrigerators can consume as many as 1,500 kWh/yr, while new Energy
Star models might use 350 kWh/yr or less. Based on the cost of electricity in your area - and the cost of a new
frig - you can calculate if it's a good payback to donate your old refrigerator and get a more efficient one.
Appliances that use electricity to make heat are very wasteful of energy, as converting electricity to heat is quite
inefficient. In this category would fall most electric stovetops, water heaters, and clothes dryers. Especially
wasteful and expensive is an "electric furnace," a central heating unit that sends electricity through metal coils
(electric strip heat). The resistance in the coils causes them to get red hot and then air is blown across these hot coils,
heating the air and blowing it into your rooms.
AIR LEAKAGE (Whole House Air Infiltration/Exfiltration)
Whenever the pressure in a home differs from the pressure in adjoining spaces (e.g., an attic, basement, outdoors), air will either
rush into the house (infiltration) or out of it (exfiltration). All that's required for this airflow is a pressure difference and a hole for the
air to flow through. "So what ?," you might ask. This uncontrolled airflow has a significant effect on energy efficiency.
During the winter, when the indoors is significantly warmer than outside, the corresponding high pressure in the house
pushes expensive heated air out of the house, causing your heating system to work overtime. In summer, hot, humid,
often dirty outdoor or attic air flows into the house toward the lower pressure air conditioned interior, causing your air
conditioner to work more than it should. During both seasons, this air leakage can cause discomfort and high energy bills.
Another problem with air leakage is that it is the classic case of convective heat transfer, the movement of heat on currents
of air. Convection also carries water vapor from outside into a house. If this water vapor makes it all the way inside, it
puts an added load on the air conditioner. If it hits a cold surface on the way in, it can condense within a wall or other
unseen place and cause a wide range of moisture problems.
Every house has leaks in its air barrier - which can be reduced by air sealing. The exact amount of leakage can be measured in cubic feet/minute by a blower door apparatus. This testing device also enables us to locate the leak points.
BUILDING BARRIERS
There are many kinds of barriers commonly discussed in building science.
-
Air Barriers
This concept is pretty straight-forward. Air barriers are intended to impede air leakage (the flow of air and the
moisture it contains) into and out of a house. Examples of air barriers include plaster, stucco, plywood and oriented strand
board sheathing, woven polyethylene house wraps such as Tyvek (if the overlapping seams are taped), and sheetrock.
These materials become better air barriers when the joints between them are sealed with caulk, tape, or foam.
The air barrier and the insulation in a house should always be touching each other, thus composing the
thermal boundary of the house. The insulation slows conductive heat transfer and the air barrier slows
convective heat transfer. These two elements joined together usually form the boundary between
conditioned space [see Conditioned Space, below] and unconditioned space.
-
Fire Barriers
The purpose of these barriers is to prevent the spread of fire within and between buildings. They include ...
-
Fire Barrier
This is a generic building code term denoting an assembly that has been certified to withstand and
contain a fire for a certain amount of time.
-
Thermal Barrier
This is a sheeting material that protects the materials on the other side of it from reaching a temperature
of 250 degrees during a fire. The classic example is 1/2 inch sheetrock.
-
Ignition Barrier
Used with foam insulation, an ignition barrier aims at preventing the foam from igniting (the first step in
burning). Ignition barriers are usually required when foam insulation is installed in uninhabited
house spaces such as attics. Such a barrier may be a material covering the foam or a
covering that is painted or sprayed on top of the foam. A few foam products have an ignition barrier in
the foam material itself. The code requirement for an ignition barrier to cover foam insulation is often
uninforced, which is lamentable to anyone who has seen foam burn.
-
Fire Partition
This is a fire barrier that retards the spread of fire between rooms on one level of a building.
-
Firewall
This is a structural fire barrier between sections of a building, designed to remain intact and standing during and after a fire.
-
Vapor Retarders
These are materials that retard the flow of water vapor, driven by differences in vapor pressure, through
building assemblies.
-
Vapor Barriers
Class I vapor retarders are called "vapor barriers," as they allow very little flow of water vapor
(less than .1 perm). Examples are polyethylene sheeting, "visqueen," aluminum foil, oil-based
primers, vapor barrier paints, and some wall-papers. A vapor barrier is sometimes used in very cold
climates between studs and interior sheetrock to prevent water vapor from traveling from inside the house
and condensing on cold surfaces inside walls. In mixed climates and in warm, humid climates,
the use of vapor barriers is discouraged because they can trap moisture where you don't want it. An
exception is the use of polyethylene under concrete slabs to prevent ground moisture from entering
the concrete and wicking up into the house.
-
Class II and Class III Vapor Retarders
These are designed to allow permeability of .1-1 and 1-10 respectively. They slow, but do not stop,
vapor diffusion through building assemblies.
-
Weather-Resistant Barriers
The classic materials for these barriers are perforated asphalt felt ("tar paper") and "house wraps" such as
Tyvek. They prevent rainwater from moving through the outer siding into the plywood or OSB sheathing.
Sometimes there is a space created between the siding and the weather barrier, a drainage plane, which
allows water to drain to the bottom of a wall and out. Weather-resistant barriers are designed to be
permeable, so that water vapor can move through them and liquid water cannot.
BLOWER DOOR TEST
Blower door testing equipment measures how much air is leaking into or out of a house, which is known as "whole
house air infiltration." A "leaky" home results in higher heating and air conditioning bills, since the leakage of expensive
conditioned air from the house or leakage of unconditioned air into the house - require the system to run longer.
Conversely, making a house "too tight" adversely affects indoor air quality and may require the addition of mechanical
ventilation to bring fresh air into the house.
Blower door test equipment is the only scientific way to measure whole house air infiltration. The equipment consists
of a vinyl "door" and frame which can be modified to fit any standard door opening. There is a hole in the door into which a
special fan is placed. When the fan is turned on, a very accurate manometer (pressure gauge) measures how much air
is leaking into/out of the house.
BORESCOPE
A borescope is an optical device consisting of a rigid or flexible tube with an eyepiece or screen on one end
and an objective lens on the other. It is used for viewing objects that are inaccessible, as when the inside of a
wall cavity is checked for mold or an evaporator coil inside a metal enclosure is assessed for blockage by dirt.
The lens end of the device is usually surrounded by optical fibers for illuminating the remote object and its
image is magnified and displayed on the other end in an eye piece or on a screen, and can be photographed.
BUILDING SCIENCE
The study of how water, air, and other gasses - driven by the forces of heat and pressure - interact in a building
to affect its energy efficiency, durability, and the safety, comfort, and health of its occupants.






BEFORE
AFTER





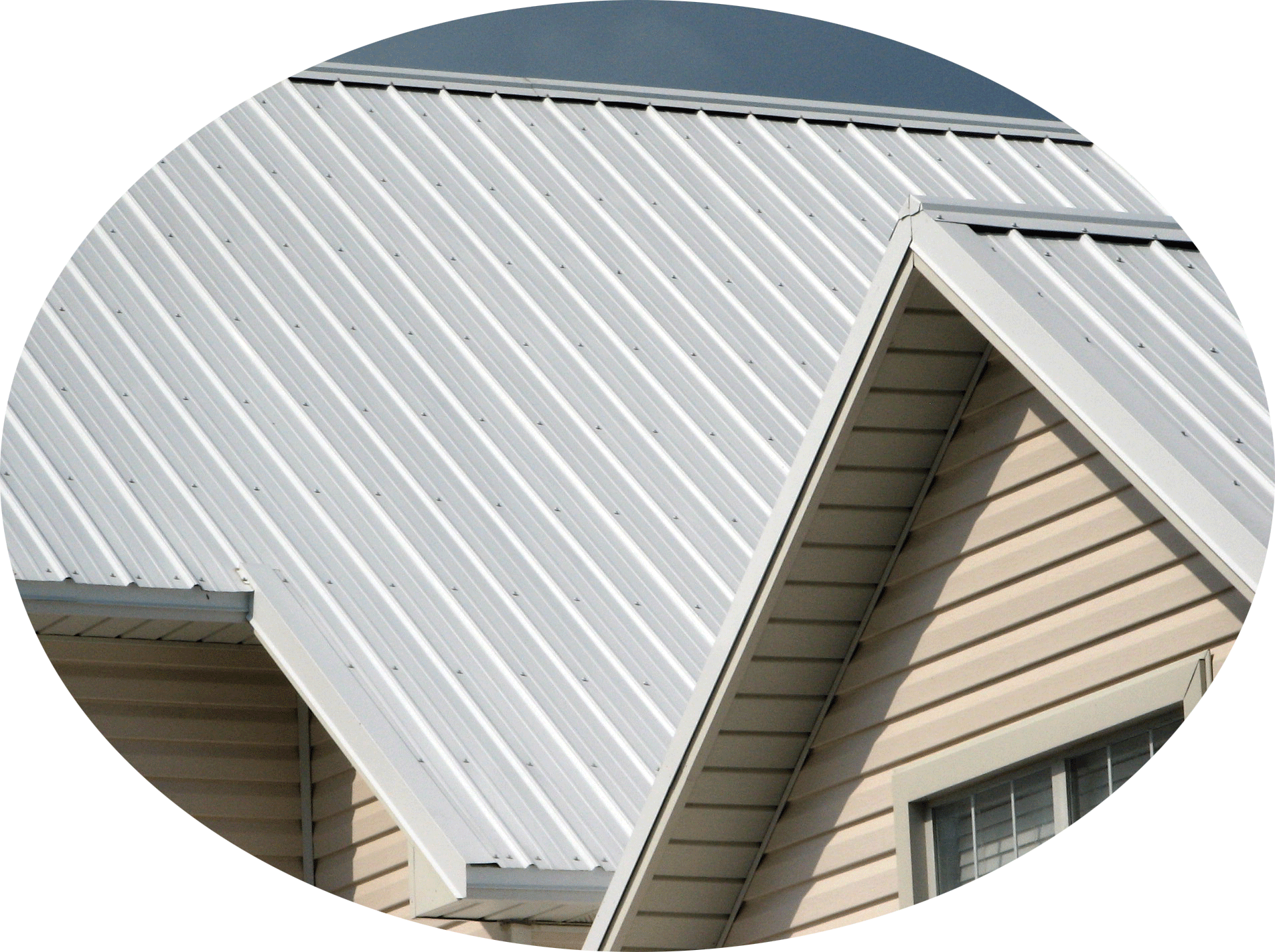






Polished Alunminum 91% 9%
White Shingle 84% 16%
Grey Shingle 25% 75%
Polished Alunminum 3%
White Shingle 93%
Grey Shingle 95%

Central Forced Air Split System
Air Flow Hood
Mini-Split System
Geothermal - Ground Source Heat Pump
Air Flow Hood
Air Barrier
Ignition Barrier
Thermal Barrier
Vapor Barrier
Weather-Resistant Barrier
Blower Door
Borescope
Semi-Conditioned Space
Cool Roof
Conditioned Space
Metal Roof

NEST THERMOSTAT
CONDITIONED SPACE
Conditioned space is that area of a house that is enclosed by its thermal boundary (formed by conjoined
insulation and air barrier) and supplied with conditioned air from the home's heating/air conditioning system.
This is the space of "indoor air," as opposed to outdoor air.
Semi-conditioned space is the term often used for an area that is within the home's thermal boundary,
but not supplied with conditioned air. An example would be an attic in which spray foam insulation has been
applied to the underside of the roof sheathing, sealing all openings to the outdoors, but which is not air
conditioned.
COOL ROOF
This is a dandy opportunity to get into some important, but subtle, aspects of heat transfer from solar radiation.
Since the majority of the heat that enters a house is from solar heat striking the roof, it is important to
understand the physics of this in order to keep roofs cool in climates that call for air conditioning much of the year.
About half of the energy from the sun comes in the form of infrared radiation, which we experience as "heat."
When this energy strikes an object on earth, the object reflects some of this energy and absorbs the rest.
Infrared energy reflected + infrared energy absorbed = 1. [Objects such as glass allow a third possibility, as
some of the energy is transmitted through them.]
Here is the approximate percentage of solar heat that three common roofing materials reflect and absorb.
Reflected Absorbed
Given the fact that polished aluminum absorbs by far the least heat, should it not be the coolest?
Why no it is not, because there is another factor to consider. All objects that absorb heat retain some of it and
emit the rest (the two again adding up to 1). Below we see how much of their absorbed heat these materials
radiate away from their surface (their emittance).
Emittance
Most objects emit about 95% of the heat they absorb, but there is a class of objects, for example, metalized materials, that give off only about 5% of their heat. Such objects are called radiant barriers.
In this example, the metal roof would not be the coolest. Though it reflects away the most heat, the amount that it absorbs continues to build up during the day because it can get rid of very little of it through emittance. The white roof reflects most of the solar heat striking it (84%) and it easily gets rid of most of what it absorbs (93%).
If you get a chance, climb onto a metal roof on a summer afternoon and experience the heat. Then do the same with a white shingle roof. Of course, you probably will not be able to find a white shingle roof because they are not in "fashion" (to wit, your neighbors would think you weird if you had one). However, if they were the default roof, the world would be a much cooler place.
COMBUSTION SAFETY TESTING
Combustion safety testing is important because many homeowners have fires burning inside the heated and air conditioned spaces of their homes, usually in the form of natural gas or propane water heaters, space heaters, oven/range tops, and central furnaces. The downside of this arrangement is that these fires never burn their fuels completely and they emit some amount of nefarious combustion gases, such as carbon monoxide and nitrogen dioxide.
The recognition of the potential problems from incomplete combustion has lead to a refinement in how combustion appliances draw (get air for combustion) and vent (get rid of their exhaust).
-
Unvented Appliances
These appliances draw in combustion air and vent combustion gases directly from/into the space surrounding them. No
attempt is made to take the gases outdoors, away from occupants. Examples are kerosene space heaters and "gas log"
natural gas space heaters that have no chimney or stove pipes carrying the exhaust out of the house. These appliances
are UNSAFE. Don't buy one. Gas ovens and range tops are also unvented, but an exhaust fan can be installed over
them to remove exhaust.
-
Vented Appliances ("Naturally" or "Atmospherically Vented")
Examples of such appliance are common gas water heaters, wood burning stoves, and fireplaces. Air for combustion
comes from inside the house and exhaust gases go up a chimney or flue (stove pipe or stack) and discharge outside the
house. These gases rise (draft) because the heated air discharged from the appliance is hotter, more expanded,
less dense, and more buoyant then the air outdoors. The strength of the draft is a factor of the height of the stack and the
temperature difference between inside and outside.
[Actually, the movement is caused by pressure differences, as
air always flows from high pressure to low pressure. Thus, the
strength of the draft can be predicted by measuring the draft
pressure within the stack relative to the pressure in the
room the appliance is in.]
-
Spillage
Naturally vented appliances always present the possibility
of their exhaust gases spilling back into the living space
rather than going up the stack to the great outdoors, an
event known as spillage. Brief spillage of combustion
gasses is somewhat normal until the stack heats up.
-
Backdraftting
Backdrafting is continuous spillage, a reversal of the
stack's normal direction of flow. This will occur if the
pressure in the zone the appliance is in is negative enough
relative to the pressure in the stack. This unfortunate
situation can be inadvertently created in a number of
ways - by turning on one too many exhaust fans, by leaks
in the supply portion of the air conditioning duct system,
by a bird's nest in the flue stack - events that cause the
house to be very negatively pressurized in reference
to the outside.
-
Forced Draft Appliances
These are appliances with a vent system in which a fan, installed at the combustion appliance, forces
combustion gasses to the outdoors by creating a positive pressure in the vent pipe.
-
Induced Draft Appliances
A vent system in which a fan - installed at or very near the termination point of the vent
pipe - moves the combustion gasses to the outdoors with negative pressure in the vent
pipe. Both forced and induced draft appliances use fans to prevent backdrafting and they are
inherently safer than naturally vented appliances.
-
Direct Vented (Sealed-Combustion) Appliances
This is an appliance in which all combustion gasses are vented to the outdoors through an
exhaust vent pipe AND all combustion supply air is drawn into the combustion chamber through
a separate, dedicated supply-air vent. These are the highest efficiency appliances. The
normal atmospherically vent gas furnace is about 80% efficient, while a
sealed-combustion unit has an efficiency of 95% or more.
This brings us to combustion safety testing, which is a series of tests to determine the presence of unburned and burned gasses in a home and the reasonable possibility of excessive levels occurring. Common testing protocols include ...
-
Gas Leak Detection
A gas leak detector is positioned next to natural gas lines, especially at seams and junctions, outdoors
at the gas meter and throughout the house where the gas lines run to stoves, water heaters, clothes dryers,
furnaces, etc. These detectors beep rapidly when they detect a gas leak, which is confirmed by applying a
soapy fluid to the suspected leak to see if escaping gas causes it to bubble.
-
Atmospheric Carbon Monoxide Testing
A carbon monoxide detecting instrument (monoxer) reads the parts per million (ppm) of CO in the air of the
house. This is especially important close to a gas oven/stove.
-
Worst Case Combustion Appliance Zone (CAZ) Testing
This is a somewhat elaborate test, the purpose of which is to create the greatest negative pressure in a
zone of the house containing a naturally drafting combustion appliance. If the pressure in the zone is
negative enough,the appliance could backdraft, spilling exhaust gas into the house. In this test, the normal
room pressure is measured to establish a baseline. Then bathroom exhaust fans, kitchen hoods, clothes
dryers, and HVAC systems are turned on to arrive at a configuration that creates the greatest possible
negative pressure. There is a pressure standard that determines pass/fail. The idea of all this is that,
according to the irrevocable law of the universe known as Murphy's Law, if the condition is possible to create,
someone will do it.
-
Spillage Test
With the combustion zone set up in the worst case negative pressure condition, an appliance such as a
water heater is turned on and tested for how long exhaust spills into the room before it (hopefully) heats
up and starts to draft to the outdoors.
-
Draft Pressure Test
Again, with the combustion zone in worst case negative pressure conditions, a pressure gauge reads
the pressure in the draft pipe to determine is it is sufficiently negative, compared to the negative pressure
in the combustion zone, to safely draw exhaust gasses out of the house.
-
Undiluted Carbon Monoxide Test
The final test in this series to insert a probe, connected to a carbon monoxide-reading instrument, into
the exhaust gas stream - before the stream is diluted with air - to determine how many ppm of carbon
monoxide are in the combustion gasses. Carbon monoxide is an unusual gas, because your blood just loves
it. The affinity between hemoglobin and carbon monoxide is approximately 230 times stronger than the affinity
between hemoglobin and oxygen, so hemoglobin binds to carbon monoxide in preference to oxygen.
That's not very reassuring, especially because carbon monoxide is colorless and odorless - and really hard
to detect without instruments.
COMFORT
A "comfortable" home is one free of such annoying stimuli as rooms that are too hot or too cold, drafty areas, high
moisture levels, stuffy air, musty odors, noisy air conditioning, and places where lighting is too dim or glaring.
COMPUTER ENERGY MODEL
The Home Energy Rating System (HERS) uses a software program (REM/Rate) developed by Architectural Energy
Corporation of Boulder, CO. Hundreds of measurements and other data entries about a home's framing, insulation,
windows, thermal mass, mechanical equipment, etc. are entered in the software, enabling it to
create a model of the building's energy use and costs - and give the home a single number for its energy efficiency
- it's HERS Score.
Once the model is built, the inputs can be changed to predict the energy impacts of different framing, insulation,
windows, etc. Thus, a new or existing home can be "improved" in the model before any physical work is done on it.
To better compare any home to the computer model's "reference home," the software aims to virtually eliminate a major factor - how the homeowner operates his/her home - from the equation. A single entry, "Number of Bedrooms," informs the model of how many people are using energy in the house.
DOORS
All fenestration (doors and windows) is a weak spot in the R-value of a wall assembly containing, say, R-13 insulation in the wall's cavities. The most common type of exterior door, solid-core wood, has an R-value of only 2.5. The other common door is composed of an insulation, such as foam, encased in metal or fiberglass, with an R-value between 4 and 7.
While insulation slows conductive heat transfer through a door, convective heat transfer (heat moving in air currents) is a factor of how well a door is sealed. Proper sealing most commonly entails some form of gasket on the door stop at the top and sides of the door. When the door closes, it compresses this gasket and makes a seal. The gap at the bottom of a door, usually the point of highest leakage, is sealed with a sweep or door bottom.
DUCT BLASTER
Duct blaster test equipment is used to test the leakage of a heating/air conditioning system in cubic feet/minute at a
pressure of 25 pascals. The equipment consists of a fan that blows air into the system and a manometer (pressure
gauge) that measures airflow. A duct blaster test is the only way to quantify the "tightness" of a system.
DUCT LEAKAGE
Although the duct blaster test is often referred to as a "duct leakage" test, in reality the leakage of the entire
heating/air conditioning system is being measured - from the return grill, through the return ducts, through the
mechanical equipment, and through the supply ducts to the supply registers (grills).
Conditioned air leaking out of the system to such places as attics is pure waste. Reducing leakage is the single most
cost effective way to reduce energy consumption in hot, humid climates. Leakage is often given as the percentage of air
leaking compared to the total amount of air presumed to be pushed through the system by the blower fan. A leakage
rate of 200 cubic feet/minute (cfm) in a system moving 2,000 cfm of air is leakage of 10%.
EFFICIENCY
This term describes the relationship between the energy put into a process and the energy coming out of that process.
Efficiency = output/Input. So, if 100 units of energy come into a process and 98 units come out as useful work, the process
is 98% efficient and has an energy factor (EF) of .98.
In a heating system of this efficiency, 100 kilowatts of electrical energy entering the system would be converted to 98 kilowatt-equivalents of heat energy exiting the system. In general, there are energy losses in every system, so there is always less energy out than in. Thus, one common statement of the Second Law of Thermodynamics is "It is impossible to convert thermal energy into useful work with 100% efficiency."
[It is useful to understand the nature of "The Laws of Nature." Many people believe that if something is a "Law of Nature," it must happen. For them, the Law of Universal Gravitation means, to put it very simply, that things fall down. They always fall, because they must. It's the law and it cannot be contradicted. This view holds natural laws as prescriptive.
In "reality," these laws are descriptive. They simply describe the observations of humans. Though humans have observed unsupported objects falling 100% of the time over thousands of years, it is still possible that the next time you release an object, it will rise upward. Formerly it was a "law" that the sun revolved around the earth every 24 hours. With further observation, a new "law" described the earth revolving around the sun every 365 days.]
ELECTRO-MAGNETIC FIELDS (LOW LEVEL)
The "official word" from the World Health Organization's International Commission on Non-Ionizing RadiationProtection is
that ...
"Although hazards from exposure to high-level (thermal) RF fields were established, no known health hazards
were associated with exposure to RF sources emitting fields too low to cause a significant temperature rise in
tissue. Biological effects from low-level (10 MHz-300GHz) RF exposure were identified needing replication and
further study."
The "biological effects" about which the WHO is unsure and that require further study include effects on genes,
signal transduction effects, alterations in membrane structure and functions, cancer promotion, DNA damage, central
nervous system function, melatonin synthesis, permeability of the blood brain barrier, reaction to neurotropic drugs,
changes to eye structure and function, pregnancy - to name a few. The report continues that, in regard to mobile
telephones and cell phone towers, "Recent studies that may indicate an increased incidence of cancer in exposed
populations [that means YOU] should be investigated further."
While we wait patiently for the results of these studies, it might be prudent (especially for environmentally
sensitive people) to avoid spending a lot of time within low-level electro-magnetic fields. These fields are easily
detected and their intensity measured with an EMF meter. Particular care might be taken to avoid sleeping for
eight hours each night with your brain within such a field.
We have found babies' cribs within very strong fields where the home's electrical service entrance was on the opposite
exterior wall, which the studies referenced above might conclude are detrimental to brain development.
In another case, a large circuit breaker box was found a foot away from the pillow of a bed on the opposite side of the
wall [see photos]. The intensity of the field was mapped on brown paper and was high enough to prompt the
homeowner to move his daughter's bed to another place in the room.
ENERGY EFFICIENCY
This is complex concept. The scientific, reductionist definition is "the total amount of 'energy' a home uses,"
measured in Btu of electricity, natural gas, propane and other fossil fuels.
The HERS Rating software models a home's energy consumption in four categories: heating, cooling, water
heating, and lights and appliances. Plugging in utility rates predicts the dollar cost of energy consumption.
Energy efficiency can be improved along two paths. Passive home design focuses on positioning a home intelligently
on its site - in reference to the sun, shade trees, wind, and drainage (earth, air, fire, water). Active design refers to home
and site elements that are "built," such as the length of roof overhangs to block sunlight and heat or using high-efficiency
air conditioning systems.
ENERGY EFFICIENT HOME
An energy efficient home is one with a good (low) HERS Score. (See HERS, below)
ENERGY MODEL (See Energy Modeling Software Entries, below, under "HERS Score")
ENERGY EFFICIENT MORTGAGES AND CREDITS
-
Energy Efficient Home Credit
This is a federal tax credit of $2,000 for builders of new site-built homes that
reduce heating and cooling energy consumption by 50% relative to the
International Energy Conservation Code (IECC) 2006. A HERS Rating is
required to verify that this energy standard has been met.
-
Energy Efficient Mortgages
An Energy Efficient Mortgage (EEM) is a mortgage that credits a home's
energy efficiency in the mortgage itself. EEMs give borrowers the
opportunity to finance cost-effective, energy-saving measures as part of
a single mortgage and stretch debt-to-income qualifying ratios on
loans, thereby allowing borrowers to qualify for a larger loan amount and
a better, more energy efficient home.
A HERS Rating is required before financing is approved to verify for the
lender that the home is energy efficient.
EEMs are typically used to purchase a new home that is already energy
efficient such as an ENERGY STAR certified home. The term EEM
is commonly used to refer to all types of energy mortgages including
Energy Improvement Mortgages (EIMs), which are used to purchase existing homes that will have energy efficiency improvements made to them. EIMs allow borrowers to include the cost of energy-efficiency improvements to an existing home in the mortgage without
increasing the down payment. EIMs allow the borrower to use the money saved in utility bills to finance energy improvements. Both EEMs
and EIMs typically require a home energy rating to provide the lender with the estimated monthly energy savings and the value of the
energy efficiency measures — known as the Energy Savings Value. EEMs (and EIMs) are sponsored by federally insured mortgage
programs (FHA and VA) and the conventional secondary mortgage market.
Lenders can offer conventional EEMs, FHA EEMs, or VA EEMs.
-
Conventional EEMs
These EEMs increase the purchasing power of buying an energy efficient home by allowing the lender to increase the borrower's
income by a dollar amount equal to the estimated energy savings. While Freddie Mac does not offer EEMS, they do allow
underwriting flexibilities for energy efficient improvements with all of their offerings.
-
FHA Energy Efficient Mortgages
The mortgage loan amount for an FHA EEM can be increased by the cost of effective energy improvements. The maximum amount of the portion of the EEM for energy efficient improvements is the lesser of 5% of ...
- the value of the property,
- 115% of the median area price of a single family dwelling,
- 150% of the conforming Freddie Mac limit.
No additional down payment is required and the FHA loan limits won't interfere with the process of obtaining the EEM.
-
VA Energy Efficient Mortgages
The Veteran's Administration (VA) EEM is available to qualified military personnel, reservists and veterans for energy improvements
when purchasing an existing home. The VA EEM caps energy improvements at $3,000–$6,000. Borrowers should ask their lender
about a VA EEM at the beginning of the lending process.
-
Additional Financing Information
To learn more about EEMs, contact Fannie Mae, Freddie Mac, the FHA or the VA. Additional information about energy-efficient
mortgages can be found on the websites for the U.S. Department of Housing and Urban Development (HUD) and the Residential
Energy Services Network (RESNET) . More information on other energy efficiency financing opportunities for homebuyers and
homeowners can be found on the U.S. Department of Energy's website.
















Unvented Appliances
Vented Appliances
Induced, Natural, Forced
Gas Leak Detection
Undiluted Carbon Monoxide Test
Duct Blaster
Circut Breaker Box
HERS Certificate
Energy Efficient Home
Energy Efficiency Mortgages & Credits

Electro-Magnetic Field Map
COMFORT
ENERGY STAR HOMES
An ENERGY STAR Home is a single or multi-family home that meets the stringent energy efficiency requirements set forth in the ENERGY STAR Certified Homes, Version 3, National Program Requirements. The builder and HVAC contractor must both be qualified by ENERGY STAR and their work must be verified by a qualified HERS Energy Rater.
There were formerly two paths to creating a certified ENERGY STAR home. Currently, there is only the ...
-
Performance Path
If a builder decides to follow this path to ENERGY STAR certification, there is some freedom to decide the level of various building
components, providing that the building achieves (performs to) a certain HERS rating score. This path also mandates that the
requirements on the checklists, mentioned above, be met. A HERS Energy rating is required to verify the building has met the target HERS
score.
ENTERPRISE GREEN COMMUNITIES
Enterprise Green Communities is the first national green building program focused entirely on affordable housing. A set of Enterprise Green Communities Criteria was created to promote the incorporation of environmentally conscious design elements and the adoption of sustainable practices into the development and rehabilitation of affordable housing. For single family and multi-family (three stories or fewer) new construction projects, ENERGY STAR certification and HERS Ratings are required.
HEAT TRANSFER
Air conditioning systems, the largest consumers of energy in hot, humid climates, work to remove heat from our homes in the summer. Heating systems add heat to homes in the winter. We pay big-time to make this happen.
Energy efficiency is achieved by reducing the unwanted transfer of heat into and out of houses, so it is beneficial to understand the physics of heat transfer.
There are three basic of ways that heat moves from one place to another.
-
Conduction
This is the transfer of heat (which is the excitement of molecules) from molecule to molecule in a solid. Conductive heat flow is slowed by
insulation.
-
Convection
Convective heat transfer is the movement of heat carried in a fluid, such as air.
Driven by pressure differences between indoors and outdoors, heat moves into
homes in hot weather and out of homes in cold weather. This infiltration of heat in the
summer on air currents is slowed by an air barrier, which closes holes that air may
pass through.
-
Radiation
This is the transfer of heat through space, in waves, between objects of different temperatures. There are two types of thermal radiation
that affect heat transfer in buildings.
-
Solar Radiation
This is heat traveling from the sun, which is approximately 10,000 degrees F, in relatively short wave lengths, to objects on earth in
straight line-of-sight. This solar heat transfer is reduced by placing something in the line-of-sight between the sun and a home, such
as the leaves of a tree to shade the roof or a white or metal roof to reflect the solar heat.
- Infrared, or earthly, radiation
This is the heat flowing to and from objects on earth of different tempeartures
(which are commonly between 0 and 2,000 degrees F) in longer wave lengths.
INSULATION
The purpose of insulation is to slow the transfer of heat by conduction. This is effected by insulation's entrapment of
air (or other gas) bubbles within its structure, which stops conductive heat transfer from molecule to molecule of the solid
material and requires the heat to transfer by radiation across the space of the air bubbles.
The degree to which insulation resists heat transfer is expressed in R-value. The higher the R-value, the higher the
resistance. [R-value is the inverse of U-value, which is a measure of the degree to which a material allows heat transfer.]
The two general types of insulation are fibrous and foam.
-
Fibrous Insulation
The most common fibrous insulations are fiberglass and cellulose.
Fiberglass
This type of insulation is made of melted glass drawn into fibers that trap pockets of air. It comes in
both batts and loose-fill forms, with R-values ranging from R-2.8 to R-3.7 per inch.
Cellulose
Recycled paper and cardboard, to which about 25% fire retardant (boric acid) is added, constitute this type of insulation. Its R-value is about R- 3.7 per inch. It's good to keep it dry, as it will absorb 1 1/2 times its weight in water.
-
Foam insulations
This type traps air and other gas bubbles inside the foam. It comes in two common forms.
Rigid Foams
This is sold in 4' x 8' sheets of various compositions
- Expanded Polystyrene
The white styrofoam of common coffee cups (R-4 per inch) which usually comes in 4' x 8' sheets.
- Extruded polystyrene
The 4' x 8' pink, blue, or green foam boards you see at Home Depot (R-5 per inch).
- Polyisocyanurate
Foam boards, in 4' x 8' sheets, covered with aluminum foil on both sides (R-7per inch).
Spray Polyurethane Foams
The most common types of spray foam are open-cell foam and closed cell foam.
- Open Cell (approximately R-3.7 per inch) is formed by the reaction of its primary ingrident, isocyanates, with its "blowing agent,"
water, to form the carbon dioxide bubbles that are the "cells" of the foam. The product expands so much that over 50% of these
bubbles burst and air fills all the open spaces in the material. It weighs about 1/2 a pound/cubic foot and is soft and somewhat spongy. It is most often used for wall and attic insulation, as liquid water can pass through it and expose any leaks in walls and roofs.
- Closed Cell foam (about R-6 per inch) is formed with the blowing agent Enovate [a typical chemical corporation euphemism for HFC-
245fa, 1,1,1,3,3 -pentafluoropropane] reacts with isocyanates to form a gas that has higher insulating values than the gas in open cell
foam. These gas bubbles, or cells, do not expand as much as in open cell foam. In closed cell foam, over 90% of the bubbles do not
break, so the cells have an independent structure and do not share walls with other cells. This makes the foam far stronger. In fact,
closed cell foams, which weighs around 2 pounds/cubic foot, actually add structural strength to a building. It is the usual choice for
insulating under the floor of raised houses, as it is nearly impervious to water in both liquid and vapor form.
The difference in moisture permeability between open and closed cell foams is important for builders to understand. Any polyurethane
foam will hold up to liquid water pretty well - compared to other building materials. They are plastics and when they get wet, they dry,
as long as they are not immersed in water so long the cell structure is destroyed. Open cell foam will take on water if exposed to a bad
leak, whereas closed cell foam performs much better, not allowing a significant amount of water to enter its cell structure.
Permeability to water vapor is a different matter. Molecules of water in gas form, water vapor, are much smaller than molecules of water in liquid form, so they pass through tiny holes. The force driving the passage of water vapor through building materials is "vapor
pressure," which is simply a difference is pressure between one side of a building material and the other. This pressure difference is
pretty constant, since there is usually a significant difference in temperature between a conditioned living space and outdoor air. Open
cell foam 5" thick (a normal thickness in an attic application) has a vapor permeability of about 10. Two inches of closed cell foam (the
typical thickness of an under-floor application) has a perm rating of around 1. Because of this far greater resistance to vapor diffusion,
closed cell foam is the usual choice under floors. If water vapor were to pass through a foam, penetrate to a cold floor, and there
condense into liquid water - a floor could buckle or rot.
The short version of all this the common statement, "Open cell is an air barrier. Closed cell is an air and vapor barrier." [For a fuller
discussion of this topic, visit www.energsmart.com.]
Polyurethane foams are composed of roughly 2/3rds methylene-diphenyl diisocyanate (MDI) and 1/3rd polyols, which are usually made from
adipic acid and ethylene or propylene oxide. Sometime polyols are made with soy, sugar cane, or caster beans. These are advertised as
"green" or "natural" foams, but the natural materials are usually less than 10% of the final insulation. To this blend are added amine catalysts,
surfactants, and flame retardants, and blowing agents.. Foam manufacturers say that this product, once it hardens, is "inert." We will see, as
data on this experiment comes in over the next 20 years.
HERS RATING - HOME ENERGY RATING
This is the standardized, national system for measuring and predicting the energy efficiency
of a home. It applies to all climate zones in the United States and is recognized and used by
the Department of Energy and other federal and state programs. In Louisiana, its use is
mandated in the Home Energy Rebate Option (HERO) Program.
HERS SCORE
Along with energy use and energy cost, the Home Energy Rating System gives the home
a numerical score - its HERS Score - that compares it to a "reference" building. This reference
building scores 100 and is roughly equivalent in energy consumption to "the standard new
house conforming to 2004 building codes."
Homes that are less energy efficient than the reference home score higher than 100 - sometimes
200 or more . On the other hand, Habitat for Humanities St. Tammany Parish - West is currently
building new homes that score in the '50s. A home that requires no purchased energy (this
usually requires solar panels) can score ZERO. This is a "net zero" home.
It is remarkably simple and often inexpensive to improve the HERS score - shorthand for
"energy efficiency" - of a home in a hot humid climate. Louisiana's HERO Program awarded a cash rebate to any homeowner who improved the HERS Score of his/her home by 30%. This level of improvement is often realized by upgrading the efficiency of the air conditioning system and making modest improvements to insulation.
Energy Modeling Software Entries
To create an energy model, hundreds of entries are made into an approved Home Energy Rating System software program. Each entry is
a data point used to inform the computer model of features affecting the building's energy consumption, such as the specifications for floors, walls, roofs, insulation, windows, etc. The complete set of entries results in an accurate model of how the home responds to its environment in terms of energy consumption.
HOT WATER SYSTEMS
The systems that produce hot water in a home are quite varied. The most common types are ...
-
Storage Tank Systems
These systems rely on a "fuel" to make the water hot and an insulated tank to store a large quantity of this hot water. Water is heated to a
pre- set temperature and the heating process stops until the water in the tank cools down. Then the heating process starts again. A well
insulated storage tank will keep the water hot longer, so it is worthwhile to add insulation to the tank by wrapping insulation around the
outside of the tank. Such insulated "blankets" usually have an R-value of 11.
-
Gas Systems
One common fuel for storage tank systems is natural gas. These systems usually have an efficiency rating of about 62% (.62 EF). The
fuel, natural gas or propane,is burned at the bottom of the tank and the exhaust gases flow (hopefully) through a stove pipe, or flue, to
the outdoors.
-
Electric Systems - Standard
These systems are the cheapest to buy and the most expensive to operate, but they do have the advantage of not producing
combustion gases. They have one or two sets of metal coils, through which electric current flows, heating the coils. This heat is then
transferred to the water. They have an efficiency of 92% or more.
[The "efficiency" rating of many electrical appliances is generally 90% or more, but this system of rating is grossly deceptive. It may be true that 92% of the electrical energy coming IN to an appliance can be converted to some useful purpose, giving that appliance a 92% efficiency. However, this does not take into account the gross waste of energy at the central power plant where the electricity is generated. There, coal or natural gas is burned, about 66% of whose Btu goe up the smoke stack to no benefit. Of the 33% or so of the fuel that has been converted to useful electricity, another 10% of that is lost in transmission and distribution. Thus, of all the Btu of heat that were consumed, perhaps only 30% surges into your electric water heater, where another 8 or so percent is lost, for a real efficiency of around 27%. Now, a gas water heater with a 62% efficiency starts to look pretty good.]
-
Electric Systems - Heat Pump Water Heaters
A new type of electric storage water heater has recently entered the marketplace. It looks like a standard
storage tank, but with an additional mechanism on the top, a heat pump. This is simply a much smaller
version of the heat pump used to heat and cool a home.The heat pump atop this water heater "pumps"
(transfers) some of the heat in the room in which it is located into the water in the tank. It has the additional
benefit (in hot, humid climates) of air conditioning the room since it is taking heat out of it. The efficiency of
these water heaters is around 235%, compared to a regular electric unit's 92%. "How can a water heater
have an efficiency greater than 100%", you may ask. This is because a heat pump water heater does not
burn any fuel to make heat. The heat is already there in the air and this heat is merely transferred to the
water. The transferring of the heat requires very little energy - in fact, only about half of the heat transfered
to the water. These water heaters move about 2.35 kilowatt-hours of heat for each kilowatt-hour of
electricity they use.
-
Tankless System
Tankless water heaters deliver hot water on-demand directly to the place it is used. There is no storage tank, where hot water waits for
someone to call for it, cooling down minute-by-minute until it loses so much of its heat that it has to be reheated again [Imagine the waste in
this process when you are away all day, or when you leave for a three week vacation.}
Tankless heaters can use either gas or electricity to heat the cold water that flows into them.
-
Tankless Gas Water Heaters
Because there are no storage "standby" losses, these water heaters achieve higher efficiencies than gas storage units. These heaters can be mounted indoors or on an exterior wall, where there is no danger of combustion gasses entering .
the home. When installed indoors, two types of venting systems are available.
- Power-Vent
These units use indoor air for combustion and use a fan to vent the exhaust gasses to the outside. Because
they use indoor air, they pull in some of the home's heated or air conditioned air.
- Direct-Vent
These units pull in air from outside the house for combustion, so they require two vents - one for intake
and one for exhaust (sometimes both vents are located concentrically within a single pipe containing an inner
exhaust vent and an outer intake vent).
- Non-Condensing
When a hydrogen fuel is burned in a water heater, one of the exhaust products is water vapor. This vapor is
highly corrosive (pH 3-5) and must be vented through special materials that can handle the acidity as well as
temperatures around 300 degrees F (such as expensive category 3 stainless steel. Hot exhaust gasses mean
that a significant amount of heat is going up the stack, rather than into the water. Non-condensing units have
an efficiency around 80%.
- Condensing
These heaters extract additional heat from the exhaust gasses and therefore exhaust cooler gasses, usually around 100 degrees F. The water vapor in these gasses condenses inside the unit. Since exhaust gas temperatures are lower, less expensive PVC piping can be used, easily able to withstand the reduced heat and corrosivity of the gasses. Because nearly all the heat of the combustion process is captured and transferred to the water, these units attain an efficiency between 90-98%.
-
Tankless Electric Water Heaters
The disadvantage of electric units is that they cost more to operate than gas models. The advantage
is that they produce no noxious combustion gasses (the combustion happened back at the power-generating plant) to escape into the house.
-
Solar Thermal Systems
These systems collect free heat from solar radiation in a fluid running through black solar "collectors" usually placed
on the roof of a house.
-
Direct or Open-loop
In these systems, potable water circulates through the collector, picks up heat, and returns directly to be used
in the house for showers, etc. Such inexpensive systems are favored in tropical locations because they are
simple and there is no possibility of freezing. In Hawaii, building codes mandate these systems on every new house.
-
Indirect or Closed-loop
These systems use a heat exchanger to transfer the heat collected by a "heat- transfer
fluid" to potable household water. The two fluids do not come in direct contact with each other. The most
efficient transfer fluid is water, which is used in drainback systems, where freezing of the transfer fluid is
prevented by forcing the fluid to drain back to a holding tank in an attic space where it is too warm to freeze.
Other systems use propylene glycol as a transfer fluid, as it is less susceptible to freezing.
HVAC SYSTEMS
See Air Conditioning/Heating Systems, above.
INDOOR AIR QUALITY
IAQ refers to the air quality within and around homes as it relates to the health, safety, and comfort of occupants. It is often stated in building science tomes that outdoor air is 7-8 times cleaner than indoor air - even in cities. This is due to the buildup of pollutants within the home.
The primary methods of improving indoor air quality are source control, ventilation, and filtration.
-
Source Control
There are many sources of contaminants in the home and the most effective way to deal with them is to remove them. A partial list includes
...
-
Second Hand Smoke
This contaminant can be eliminated simply by preventing tobacco smoking within the house.
-
Carbon Monoxide
This colorless, odorless, deadly gas results from incomplete combustion of fossil fuels. It can be eliminated by replacing heaters with
non-combustion models, tuning appliances for more efficient combustion, and by ensuring that combustion gasses leave the house. CO
comes from ...
- Wood-burning Fireplaces and Stoves, especially when the fire burns down and only glowing ashes remain. If you want to burn
wood in your house, be sure the chimney or flue exhausting combustion byproducts is clean and draws well - and have someone
measure the air pressure near the stove to make sure that, if it is a negative pressure, the pressure is not high enough to cause
backdrafting, a condition in which exhaust gasses flow back into the house. [see Combustion Safety Testing, above] It is also a
good idea to install a digital carbon monoxide monitor/alarm on every floor, especially near your bedrooms.
- Undrafted Space Heaters
These products, very popular in the past, burn natural gas, propane, or kerosene. They have no exhaust pipe to vent the combustion
fumes to the outdoors; they pour exhaust directly into the house. Another example is the use of the kitchen oven and/or range top
burners to heat the house. If you have an unvented combustion appliance in your house, get rid of it. It is a potent safety hazard.
One day these appliances will be outlawed.
- Naturally Drafted Combustion Appliances in Conditioned Space
"Naturally drafted" means the appliance has a stovepipe to draft combustion byproducts up and out of the house and that this
drafting occurs naturally from the fact that hot air will rise up the pipe. This drafting process is not assisted by a fan. If such an
appliance is in unconditioned space, - a ventilated attic, for instance - there is little concern that exhaust will find its way back into the
house. However, if that appliance is inside the space in which you live, such as a gas water heater in your laundry room, there is a
possibility that exhaust can come into the house. If you have such an appliance in conditioned space, you might want to ensure your
family's safety by getting combustion safety testing done on your house and by installing a digital CO monitor/alarm.
-
Volatile Organic Compounds
VOCs are gasses emitted by many furnishings and products in modern houses (off-gassing). These include ...
- Paints, varnishes, and waxes all contain organic solvents. - Household cleaning products often contain organic chemicals. Tea
tree oil is a good naturally occurring disinfectant to substitute for chlorine bleach and other strong chemical cleaners.
- Cabinets, floors, plywood, and OSB usually contain glues containing formaldehyde.
- Carpets act as air filters and can pollute your home in three ways.
> They emit VOCs from the carpet's backing and adhesive, which may contain styrene, 1,2-dichloroethane, ethyl benzene,
toluene,1,20 trichloroethane, and xylenes.
> If conditions are right, mold growth can begin within 24 hours of a spilled liquid being left undried in a carpet.
> Carpets attract filth, especially if you have indoor pets. They collect dirt, dust mites, dander, hair, etc. and hold them in your
environment. You might notice when you remove carpet that it is 2-4 times heavier than when you installed it. Ever wonder
what all that extra weight is ? If you are interested in excellent indoor air quality, or if you have greater than normal sensitivity
to pollutants, you might consider a home without wall-to-wall carpet. If you want rugs, get unbacked area rugs that can be
more thoroughly cleaned and exposed to sunlight. Exquisite oriental caprets are a good choice.
- Chlorinated drinking water releases chloroform when hot water is used. Taking a nice hot shower with such water creates
exposure. Inexpensive chlorine filters can be installed at the showerhead to eliminate this risk.
- Gasoline powered tools, stored in garages that are attached to a house that does not have a good air seal between the two
spaces, can easily leak gasoline fumes into the house. Whenever the pressure in the house becomes negative compared to the
garage - as frequently happens when air conditioning fans and exhaust fans come on - fumes from a garage, where the pressure is
more positive, can bepulled in through the multiple holes between the house and garage.
- Spray foam insulation is said by the industry not to off-gas a few days after it hardens. A practical rule of thumb is to trust your nose. If you can smell something, that means it's in the air.
-
Mold and Other Allergens
These biological contaminants are listed under source control because they can be prevented from ever arising. They require water to grow, so care should be taken to keep your home relatively dry by controlling ...
- Bulk water intrusion from leaking roofs, windows, and walls and from broken pipes.
- Air infiltration into the house from numerous gaps and holes in the air barrier of the building envelope.
Air entering the house often contains a good bit of moisture, so a "tight" house is important in
controlling the potential for mold growth.
- Poor dehumidification by the air conditioning system is a primary cause of high relative
humidity, which creates an environment for microbial contaminants. A $5 relative humidity gauge
can inform you of the actual condition in all the rooms of your house. A relative humidity of 45%-55%
is desirable. Rh above 60% should be reason for action.
-
Bacteria
- Perhaps the most famous bacterium present in indoor air was the waterborne bacterium Legionella,
which became airborne when passing through a showerhead, causing Legionnaire's Disease.
- A large fraction of the bacteria found in indoor air are shed from humans. These include
Mycobacterium tuberculosis, Staphylococcus, and Streptococcus pneumoniae.
-
Isolation
Another way to deal with pollutants that might enter the home is to isolate them by putting a barrier
between them and your home.
-
Radon
This is an invisible radioactive gas/dust created by the decay of radium found in rock formations
beneath buildings. You can't remove the rocks (source control), but you can create a barrier
between the soil and your house, thereby isolating the radon. This is typically done by installing
a vapor barrier such as cross-linked polyethylene beneath a concrete slab or on top of the
ground in a crawlspace.
-
Ventillation
A third strategy that is very effective - and free - is to ventilate your house. .
-
Opening Windows
This old-school approach brings fresh air into the house, diluting polluted air. If the outdoor humidity is not super-high where you live, you can open your windows and turn on the central A/C fan (just the fan, not heating or cooling) to circulate the outdoor air into all the recesses of your home.
-
Mechanical Ventilation
This is another way to introduce fresh air into the house and is highly recommended if your house is well-sealed (tighter than .35 natural air changes/hour). It involves bringing outdoor air into the home by mechanical means, such as fans. [see Ventilation, below]
-
Filtration
The final line of defense against indoor pollutants is filtering them out of the air. Particulates of all kinds can be trapped in filters, including pet "by- products" and attic debris (dirt, dust, fiberglass particles from insulation, etc.) that is sucked into the A/C system through leaks in the return ducts and that bypass the filter.
-
Central Heating/Air Conditioning Filters
Good filtration in your A/C system can help filter particulates, but this can happen only if the air goes through the filter. If there are unsealed places between the return grill and the fan in the system, unfiltered air is sucked into the system and distributed to all the rooms of your house. "But what about the filter in the attic A/C unit? Won't that filter
the air?" Why, yes, it would, but in many A/C systems, the installer has removed the
filter, knowing that most homeowners will not go into the attic and change it.
Thus they are relying on the filter behind the return grill to do the work. If your
return grill is in the ceiling, very close to the fan, this is no problem. But if your
return grill is in the wall, and the shaft up to the attic A/C system is poorly sealed,
you can count on dirty air getting to the unit.
If you decide to beef up your A/C filter, get some expert advice from an HVAC
professional first. It is easy to install a filter that is hard for the air to get through,
thus increasing the static pressure your air conditioner must labor against.
-
Room Filters
These are free-standing units that are good for room air filtration. You can get
very fine filtration, including HEPA filtration, from some models, whose fans are
designed to handle the static pressure.
-
De-Humidifiers
Many building scientists consider excess water to be the preeminent pollutant,
because of the damage it can do to human health and comfort and to building
materials. If your home gets extremely wet from a bulk moisture intrusion, a
commercial dehumidifier can eventually dry it out. If your home's relative humidity
is too high under normal circumstances, a good A/C professional can evaluate
why the A/C system's evaporator is not removing enough moisture from the air and perhaps fix the problem. If this is not feasible, he or
she can add a dehumidifier to the system.
-
House Plants
Studies by NASA have shown that some indoor plants, together with the medium in which they are grown, can reduce components of
indoor air pollution, particularly such VOCs as benzene, toluene, xylene, aldehydes, and ketones, as well as carbon dioxide. Plants also
produce oxygen and add a level of chi, or energy, to the environment. However, if the house has too high relative humidity, house plants could exacerbate the problem.













Solar Thermal System

Heat Pump Water Heater





Mold


Filter


Tankless Gas Water Heater

LIGHTING
Lighting falls into the general functional categories of ambient lighting (for security and safety), task lighting (to illuminate the space where tasks are performed), and accent lighting (usually on walls to make a space more visually comfortable).
Other distinctions in lighting include ...
-
Efficacy
This is a term denoting the efficiency of lighting, again comparing energy- in to energy- out, in this case lumens per watt. For example, a 100 watt incandescent lamp (bulb) produces about 1,750 lumens, giving it an efficacy of 17.5.
-
Illumination
llumination is the distribution of light on a horizontal surface and is measured in footcandles. A footcandle of illumination is one lumen distributed over one square foot.
-
Color Rendering Index
This is the degree to which the color of light from a lamp resembles the color of sunlight. Incandescent lighting has a color rendering index of 97-100, almost the same as sunlight. Compact fluorescent lambs have a range of 81-90.
-
Lighting Types
The most common types in residential use are ...
-
Incandescent
This century-old technology is still prevalent in homes, despite the fact that is very inefficient, with an efficacy of 10-23. As an electric
current passes through a tungsten filament, approximately 10% from the energy output of this type of lamp is in the form of light; the rest
in the form of heat. A halogen incandescent lamp is filled with halogen gas, enabling it to operate at higher temperatures and efficacy.
-
Compact Fluorescent (CFL)
Light bulbs (lamps) of this, now-common type are 3-4 times more efficient than incandescents and their life is about 10 times longer.
When they are energized, a small amount of electricity excites mercury vapor in the bulb, producing short- wave ultraviolet light, which
causes a phosphor coating on the glass to glow. Because of the mercury in the bulb, it is prudent to hold your breath if you break one.
-
Light Emitting Diode (LED)
LEDs are tiny bulbs that have no filament and do not get very hot. They are illuminated solely by the movement of electrons in a
semiconductor material and, unlike incandescent and fluorescent lamps, they emit light in a targeted direction. They last 6 times longer
than CFLs and are twice as efficient.
-
Light Quality
Light quality describes how well people in a lighted space can see to do visual tasks and how visually comfortable they feel in that space. The elimination of glare is essential for light quality. Direct glare is strong light from a window or bright lamp shining directly into your eyes. Reflected glare is strong light reflected off a shiny surface into your eyes. Veiling glare is glare from a work surface such as a computer
screen.
A general good practice for designers of interior spaces is to hide a light source from direct line-of-sight. Can lights recessed in a ceiling often
allow the light source (the light bulb) to be seen by occupants. This confuses the pupil of the eye, which attempts to open up to let in enough
light to see the task at hand - and to simultaneously close down in response to a bright light source in direct line of sight. These two conflicting signals can result in discomfort. If recessed cans lights must be used, it is good practice to install very deep cans so that bulbs can
be recessed deeply in them and not seen directly. The goal is to provide illumination without seeing the bulb. This concept seems
foreign to designers of outdoor (street) lighting, who usually create lighting that exposes the bulb, thus creating glare that makes it more
difficult to see both the lighted area. and the night sky. An organization called The International Dark Sky Association was created to educate
citizens and governments about this subject and has created model lighting ordinances that are being adopted by more conscious
communities.
PASSIVE HOME DESIGN
Unlike active solar design, which might use solar PV systems to increase the energy
available in a home, passive design attempts to reduce energy consumption simply by
the way a house is designed. These design principles include making the house compact
in shape to reduce surface area, orienting the building with its long axis running East/West,
reducing solar heat gain with shade trees and vines, using cool roof design, superinsulation,
thermal mass, advanced window technology, air tight building envelopes, and
natural ventilation.
RADIANT BARRIERS
A radiant barrier in residential construction is a reflective metalized material, often an aluminum foil, or the powderized metal coating used in "low-e" windows, and metal surfaces roof. Radiant barriers emit (give off by radiation) only 5% of the heat they absorb. The physics of radiant heat transfer describes how radiant barriers work. [see Cool Roof, above]
In an existing home, 4' wide foil, with tiny holes punched in it to allow water vapor
to pass through, can be stapled to the attic side of the roof rafters.
When solar radiation strikes the roof, the shingles (which for some inexplicable
reason are dark) heat up. This heat moves by conduction to the felt paper
underneath, thence to the plywood or OSB roof sheathing. At that point, the heat
reaches an open space, which it can move across only by radiating. As heat is
radiated to the foil radiant barrier attached to the underside of the rafters, most of
the heat is reflected back to the roof. The remaining heat is absorbed by the
radiant barrier, which - because of its low emissivity - holds onto most of this heat,
emitting only 5% of what was absorbed into the attic below. Note that this radiant
barrier application has two airspaces, one on either side of the barrier, thus
allowing for both reflection on one side and low emission on the other.
In a roof of a new building, the plywood or oriented strand board roof sheathing
can have a film of aluminum foil bonded to it at the factory. There is no airspace
between the aluminum barrier and the roof above it, so no heat will be radiated
or reflected back toward the outdoors. There must be an air space for this to occur.
Thus the radiant barrier will heat up more than in the example above. Still, of the heat the barrier absorbs, only 5% or so will be radiated into the attic.
One further advantage of radiant barriers in roof assemblies is that the air spaces adjacent to them have higher R-values than air spaces bordering other building materials (R-1.35 verses R-.68). Thus radiant barriers have a slight insulating properties, as well. However, this insulating air film must be relatively calm to be effective - a "dead air" space. If there is air movement in this space, from convective currents, for example, the insulating value is largely lost. For a description of how radiant barriers work in modern windows, see Windows, below.
R-VALUE
This is a measure of the resistance to heat transmission and is used to rate the effectiveness of insulation. It is the inverse of U-value.
SOLAR PHOTOVOLTAIC SYSTEMS
Solar PV systems fall into the realm of energy production rather than energy conservation. These systems are located on or close to the house and generate electricity for the house.
Before installing such a system, the intelligent step is to first reduce your energy consumption. Take an inventory of all house functions that require electricity, quantify how much each function uses, and see if you can reduce this use. For instance, if you have a lot of items that are always on standby, ("phantom loads"), such as audio/video equipment, computers/printers/monitors, etc., that are drawing current even when you are sleeping, plug them into an auto-off surge suppressor. If Uncle Fred left you his retro 1935 Norge refrigerator, which uses 2,000 kWh/yr, consider it having bronzed and replacing it with an Energy Star model.
Not reducing your electrical load by eliminating waste before installing a solar PV system is analogous to running in more and more water to fill your bathtub and ignoring the fact that the stopper is missing. If you reduce your electrical load, then any given size PV system will handle a greater percent of your needs. Be wary of solar PV companies that do not first do a load calculation and recommend ways you can reduce the load.
-
Types of Systems
Two basic system types are ..
-
Grid-Tied Systems
These systems have no batteries to store the electricity generated so
it can be used use at night or when the electric grid goes down. In
essence, the electric grid is your battery, since whenever you are
not producing enough electricity to meet your home's needs, the
extra current comes in from the grid. This is handy, as it avoids the
cost and hassels of batteries as well as certain system losses. The
downside is that when the grid is down, you are too, because these
systems have a safety feature that automatically disconnects your
inverter,which youneed to convert the DC power generated by the panels
to AC power used in your house. This "safety feature" is sold as
protection for line workers from being shocked as they toil away restoring
electrical service. [It is possible that a civilization capable of putting people
on celestial objects and then returning them home is also capable
of guaranteeing that no power can flow to the grid during a power
outage - and still allow your own generated power to be used by your local house system. I suspect this has more to do with utility
companies' machinations than with unsophisicated technology.] Many homeowners envision selling the extra power they produce back to their electricity company,since the power flows both ways. But the utility companies have good lawyers, so it's not that simple. Each utility has its own net metering agreement with its ratepayers. With many agreements, the utility will pay you (that is, credit you toward what you owe them) for the electricity you feed back into the grid, but they will do so at a lower cost than what they charge you, often half as much. Utilities often support home power generation in their PR campaigns, but in the long run, you "empowering" yourself threatens their basic business model.
-
Off-Grid Systems
This type of system is for those who want to be "off the grid." If your home is in
the middle of the woods, this one's for you. Direct current (DC) power is
produced in the solar panels and stored in batteries. When the house needs
power, the DC power is drawn from the batteries, runs through an inverter where
it is converted to AC power, and then into your house to feed AC appliances.
To be more efficient, you can buy appliances that run on DC power.
-
Hybrid Systems
These combine the best of the two systems above, as they are basically grid- tied
systems with some extra battery storage. Battery-based grid-tied inverters make
these systems possible, as they can direct power to and from battery banks, as
well as synchronize with the utility grid. In hybrid systems, fewer batteries are
needed than in off-grid systems, since the grid itself is your battery most of the
time. In addition, your electric car (a battery on wheels) can serve as a battery
too. If it's okay with your utility, you also have power during an outage on the grid.
-
System Components
Different systems have different components (some include automobiles batteries).
Below are two components common to all solar PV systems.
-
Solar Panels
Solar panels use light energy (photons) from the sun to generate electricity. They are of various physical materials, shapes, sizes, and
efficiencies and generally produce between 100-320 watts. Multiple panels are grouped in arrays, which are installed on roofs, on various raised supports, and even on the ground. Arrays can be stationary or move to track the sun.
-
Inverters
Solar panels produce direct current and your house uses alternating current, so there is an inverter in the system to convert DC to AC.
Given the current level of sophistication of solar photo-voltaic electricity generation, and the fact that efficiencies are going up and prices coming down, it is inevitable that on-site electrical generation will become the dominant technology on earth. Centralized power generation is a dinosaur whose extinction will be a blessing. These huge centralized plants ...
-
Burn fossil fuels, often dirty coal, adding both pollutants and greenhouse gasses to the atmosphere. These environmental costs are "externalized," i.e., you pay for them, not the utility.
-
Waste energy, since only about 1/3rd of the heat energy consumed is converted to electrical energy. The rest is wasted up the smoke stack. In transmission and distribution to your home, another 10% is lost (10% electricity loss is 30% Btu of original fuel lost).
-
Are unreliable, as local or area storms of all kinds can knock them out for days or weeks (try months, as in the case of hurricane Katrina).
-
Are ugly to look at, if you consider the aesthetic impact of a cityscape dominated by electric poles and their oppressive cobweb of electric wires running in every direction. This lack of even a vestige of aesthetic consideration, much less artistry, is imposed on us without our input. Upscale subdivisions bury them underground so people don't have to look at them.
U-VALUE (U-FACTOR)
This is a measure of heat transmission, specifically of how much heat passes through a 1 square foot area of a material in one hour, when the temperature difference on the two sides of the material is 1 degree F. It is the inverse of the R-value.
VENTILATION SYSTEMS
Humans benefit greatly from fresh air in their houses. Most homes in the United States leak in plenty of air from the outdoors (some clean, some not) through infiltration, which is the entry of air from locations we do not control. If a house runs a negative pressure, air will enter it from outside the conditioned space, which might be from the outdoors, from an attic, or from the musty space under a raised house. So, how do you know if your home is leaking sufficient air to maintain reasonable indoor air quality?
-
Minimum Ventilation Requirements
The standard way to calculate the amount of air a house needs is promulgated by the American Society of Heating, Refrigerating, and Air
Conditioning Engineers (ASHRAE). ASHRAE's Standard 62-1989 recommends that homes have air leakage of at least.35 air changes per
hour under natural conditions. If the leakage is less than this, mechanical ventilation is recommended. Leakage of .35 natural air
changes per hour means that all the air in a house would be displaced by new air every three hours. This changing of the air is driven by
pressure differences in the house created "naturally" (without a fan) by two non-human forces. These natural pressures are called "the n
factor" and are expressed as a number.
-
Stack Effect
Warm air is less dense than cool air and this density difference causes warm air to rise up and out through openings in the top of a house and cooler air to enter through gaps in the lower part of the house. Thus, in a two story house, the second floor would be under positive pressure, the ground floor under negative.
-
Wind Pressure
Wind creates a positive pressure on the windward side of the home and negative pressures on the leeward side - in reference to the
home's interior. Thus, wind pressure both pushes air into the home and pulls it out of the home (which, in turn, causes even more air to
come in).
There are a couple of other, human factors that affect home air pressure, including ...
- Exhaust Pressures
This is a negative pressure created in a house as air is drawn out by exhaust fans, clothes dryers, kitchen vent hoods, and
chimneys.
- HVAC Pressure Differentials
The powerful fans in heating/air conditioning systems can create pressure imbalances due to ...
> Differences in air flow, as when conditioned air is supplied to a bedroom that is tightly closed up and an equal amount of
air cannot get back to the return air grill. This causes high pressure in the bedroom and low pressure in the room where the
return grill is located.
> Differences in duct leakage, for example, when the supply ducts are leaking more than the ducts that return air from the
rooms back to the A/C equipment. This causes a negative pressure in the house.
-
Calculating the Minimum Ventilation Requirement
There is a spiffy formula for calculating how much air should be coming into a given house - two formulas, actually. One is based on the volume of the house; the other, on the number of people living in the house. To be safe, whichever calls for the most air is used.
Here's how to calculate how much air should be entering a house with a volume of 18,000 cubic feet, with
three occupants, based on the recommendations of the ventilation scientists.
MVR = .35 air changes per hour x volume of house
60
MVR = .35 x 18,000
60
MVR (expressed in cubic feet per minute) = 105 CFM
Now we make the calculation based on the number of people living in the house.
MVR = 15 CFM x number of occupants
MVR = 15 CFM x 3 people
MVR = 45 CFM
To be conservative, the larger requirement is used, so it has been calculated that this
house should be infiltrating at the rate of 105 CFM in order for it to achieve .35 natural
air changes per hour, or one complete change of air every three hours. If it is not, mechanical ventilation is recommended.
We have a problem. How can it be determined if the house is, indeed, sucking in 105 cubic feet of air every minute ? Do we hire a flock of
mice, armed with tiny flow measuring gauges, to take their stations at the 3,872
holes in the house through which air is entering ? In fact there is no way to
measure the precise inflow of air under natural conditions, so we have to use
something we can measure and try to calculate our way toward the natural
CFM flow rate we have calculated above.
This is where the blower door test equipment, with its calibrated fan, comes in
handy. [see Blower Door, above] The blower door can accurately measure the
amount of CFM the house is leaking when it is depressurized with a fan to -50
pascals (a metric unit of pressure). So, what building scientists do is translate the
minimum ventilation requirement of 105 cfm into a measurable blower door
number. They do this by multiplying the minimum ventilation number by the
n- factor, explained above.
For each climate zone (hot humid, hot dry, marine, etc.), the Department of Energy
has made a generalized calculation of what the wind pressure and stack pressure
would be in that zone and ascribed a number to each of these pressures.
Multiplying the wind pressure number in each climate zone by the stack pressure number yields the n-factor number.
In New Orleans, which is in zone 3, the n-factor number for a single story house (stack effect) that is normally-well shielded from the wind
(wind effect) is 21.5. Multiplying the minimum cfm the house needs by the n-factor translates the unmeasurable minimum ventilation rate
under natural conditions into a measurable blower door number.
105 cfm x n-factor of 21.5 = blower door number of 2,257
Leakage of 105 CFM natural = leakage of 2,257 CFM at a pressure of 50 pascals
Presto, there we have it. We turn on our blower door and if the pressure we read is above 2,257 CFM , mechanical ventilation is not
recommended. If the reading is below 2,257 CFM, the house is so tight that mechanical ventilation is recommended.
-
Mechanical Ventilation Systems
When mechanical ventilation is desired, homeowners have
three choices.
-
Exhaust Ventilation
This strategy employs a fan or multiple fans to pull
indoor air out of the house, which is replaced by
(hopefully) outdoor air infiltration. Spot ventilation
uses simple fans in bathrooms to accomplish this.
Whole house exhaust ventilation uses a larger
central fan to take air from several rooms, often the
rooms with the most moisture, such as bathrooms
and kitchen. These systems cannot control the
quality of the air that enters to replace exhausted air,
since air comes in, unfiltered, through the myriad holes
in the building envelope, sometimes from the attic and
crawl space underneath the house. The exhaust
strategy works best in cold climates, where there is
more moisture in the house than outside it, because it
prevents moisture accumulation in the house.
-
Supply Ventilation
This strategy uses a fan to bring outdoor air into the
house, forcing indoor air out through leaks in the
building envelope. The incoming air often goes
through a filter and then enters the return side of the
central A/C system. It is dried and cooled and then
blown into the rooms through the duct system. This
strategy is appropriate for hot, humid climates, since
the air supplied is filtered, heated or cooled as needed
and dried by the HVAC equipment.
-
Balanced Ventilation
A combination of the exhaust and supply systems is called a balanced system. These systems bring fresh outdoor air in and exhaust an
equal amount of stale air, thus avoiding pressurizing or depressurizing the house. In very hot and very cold climates, balanced systems often include a heat recovery ventilator. This is a heat exchanger that tempers the air coming into the house from outdoors. In cold
climates, warm indoor air being exhausted transfers some of its heat to the cold air coming in. In hot climates, the cold air conditioned
air being exhausted absorbs some of the heat from the hot air coming in, lowering its temperature. In humid climates, energy recovery
ventilators are used. These are heat recovery ventilators which also remove some of the humidity coming in.



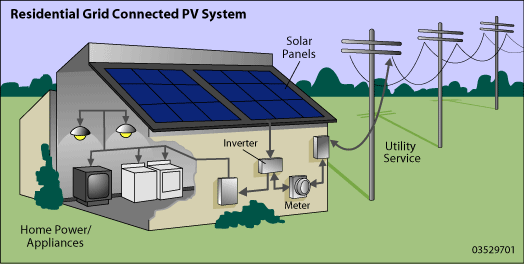


Stack Effect
Wind Effect



Supply Ventilation
Exhaust Ventilation
Mechanical Ventilation Systems
WATER QUALITY
The quality of the water we ingest is a key aspect of the "health" of our homes. The water we drink,
can be tested and then improved by stand-alone and whole-house water purifiers, and by devices that make it more
alkaline. We are also impacted by the chlorine we inhale while showering, which can be reduced or eliminated
by simple showerhead filters.
WINDOWS
From the perspective of the energy efficiency of a wall assembly, windows are potentially the weakest point. If we
have a wall with wooden lapped siding, 2" x 4" wood studs, R-13 fiberglass batt insulation in the cavities between
studs, sheetrock on the inside, and an air film on either side - that wall assembly might have an overall R-value
of R-12.
Then, let's say, we add windows - lots of windows. We live in a beautiful place and we like light so we add
windows comprising 20% of the wall, which is not unreasonable. If we install nice old single pane glass windows,
with an R-value of R-1, the R-value of that wall assembly just plunged from R-12 to R-3.75. That's a huge drop.
In addition to the drop in R-value, which is a measure of heat flow by conduction, those single pane glass
windows will allow 87% of the solar heat striking them to enter the house. Thus they are poor at slowing heat
transmission by radiation. If we installed authentic old windows from a Southern mansion, which will probably
leak in a considerable amount of air, we have now introduced a lot of heat transmission by convection.
The windows will look beautiful, but they will allow heat to move in during the summer and out in the winter by
all three modes of heat transfer. So buy a big air conditioner and furnace. Windows are rated for their energy
efficiency and other properties by the National Fenestration Rating Council and their performance is printed
on little stickers attached to all new windows. These tags report on four aspects of the window.
-
U-Factor
The u-factor, or U-value, is a measure of how much total heat the window transmits by all three forms of heat transfer - conduction,
convection, and radiation. This is arrived at by taking a weighted average of the different components of the window (the frame, the edge of
the glass, the center of the glass). Since it is the inverse of R-value, the lower the number the better.
Though U-factor deals with both frame and glass, a wooden window and a vinyl window have identical glass, so the frame itself might
be the more important consideration. Materials used for window frams vary considerably in how much heat they conduct. Aluminum frames
may have an R-value (used here instead of U-factor, since more people can relate to R-value) of R-.6. Wooden and vinyl frames are closer to
R-3- which is 5 times the thermal efficiency of aluminum. In cold climates, U-factor is the most important consideration in choosing windows.
-
Solar Heat Gain Coefficient
This is a measure of the amount of radiant heat the glass in a window allows to
pass through it, as well as the heat it absorbs and re-radiates indoors. The
amount of this radiant heat is given as a percentage of heat transmitted
compared to the total amount falling on the window at 90 degree angle. Thus
single pane glass has a SHGC of .87, which means that it allows 87% of the
radiant heat striking it to get into the house.
"Good" windows can have a low or high solar heat gain coefficient. It
depends on the climate you live in. In Northern climates, where the emphasis is
on keeping a home warm, it is desirable to let a lot of heat pass through the
window, since it helps heat the house. Thus good Northern windows might have
a SHGC of .75, indicating that they allow 75% of the radiant heat striking them
to get into the house. In the deep South, where the name of the game is to
keep the heat out, low solar heat gain coefficient windows are used. A
good Southern window might have a SHGC of .30. In mixed climates,
with more balanced requirements for heating and cooling, knowledgeable
architects specify different SHGC windows for different sides of the house,
depending on their orientation to the sun.
In hot climates, solar heat gain coefficient is the most important consideration in choosing windows.
Since solar heat gain coefficient has to do with the glass portion of a window - and since glass is glass, the same in every window, how can
some windows let in a lot of heat and others very little ? The answer is that glass can be coated with materials that can either block radiant
heat, allow it to penetrate the glass, and even retain radiant heat once it enters the house. This brings us to ...
-
Low -E Windows
The "E" in Low-E windows stands for emissivity (a concept we have already encountered in the sections Cool Roof and Radiant
Barriers, above). But emissivity is not the only physical property affecting solar radiant heat passing through the glass, as reflectivity is
important too. Low-E windows are double pane windows with one of the two interior surfaces coated with a powderized metal, either
silver or tin-oxide.
-
Placement of Metal Coatings
This metalized coating is placed on different surfaces of the two pieces of glass in a double pane window, and these surfaces need to
be named in order to understand this explanation. Surface 1 is the surface of the outer pane of glass, facing the outdoors. Surface 2 is
the other side of that piece of glass, facing into the air space between the two panes of glass. Next is surface 3 on the inner pane, also facing into the air space. Then surface 4 faces into the house. The low-e coating is not sprayed onto surface 1, because it could be
damaged by outdoor objects brushing against it. Nor is it on surface 4, since it could be abraded by people on the inside.
- Low Solar Heat Gain Coefficient Windows
These windows, used in the South where the objective is to keep radiant heat out, have their low-e coating on surface 2. Solar
radiation strikes the window and much of the heat is reflected back out by the metal coating. Of the heat that is not reflected, but
absorbed by the metal coating, only 5% is emitted into the air space between the two panes, so little heat actually gets into the
house.
- High Solar Heat Gain Windows
These windows, designed for cold Northern climates, are designed to
allow more radiant heat to penetrate them and then to retain as much of
that heat as possible. Their coatings are lighter to allow more heat
gain and they are located on surface 3. Solar radiation strikes the window, some
of which is reflected back out, some passes through into the house, and
some is absorbed by the low-e coating. Of the heat that is absorbed,
only about 5% is emitted back into the air space between the two glass
panes. The rest passes through the glass toward the inside by conduction.
When this heat reaches surface 4, it then radiates into the room. In
addition, all the objects in the room are being heated, by the radiant
heat coming through the window and by the furnace in the house.
These objects are radiating their heat in all directions, including toward the glass window. When their radiant heat strikes the
inside of the window (surface 4), some of it is reflected back into the room by the low-e coating on surface 3. Some of this heat is
absorbed on the surface 3 coating, only 5 % of which is lost to the airspace between the two panes. Thus high solar heat gain
coefficient windows allow more heat in and prevent much of that heat from escaping out the window.
-
Visual Transmittance
Another value for windows given on the NFRC's tag refers to the amount of light that passes through a window compared to the amount that
strikes it. This term refers to light, not to heat.
-
Air Leakage
The final factor on the Fenestration Council's tag is air leakage. This is usually a function of the quality of the
window's weather stripping. Additionally, some types of windows seal better than others because of their
design. Casement and awning windows are the tightest, because the window frame closes against a gasket,
compressing it for a tight air seal. The felt weather stripping of the various types of sliding windows does not do
nearly as good a job.
Air Leakage is generally less important than U-factor and solar heat gain coefficient in regard to energy
efficiency, unless the windows are old and in disrepair, as in the case of some single and double-hung windows
with large gaps between the two frames.




